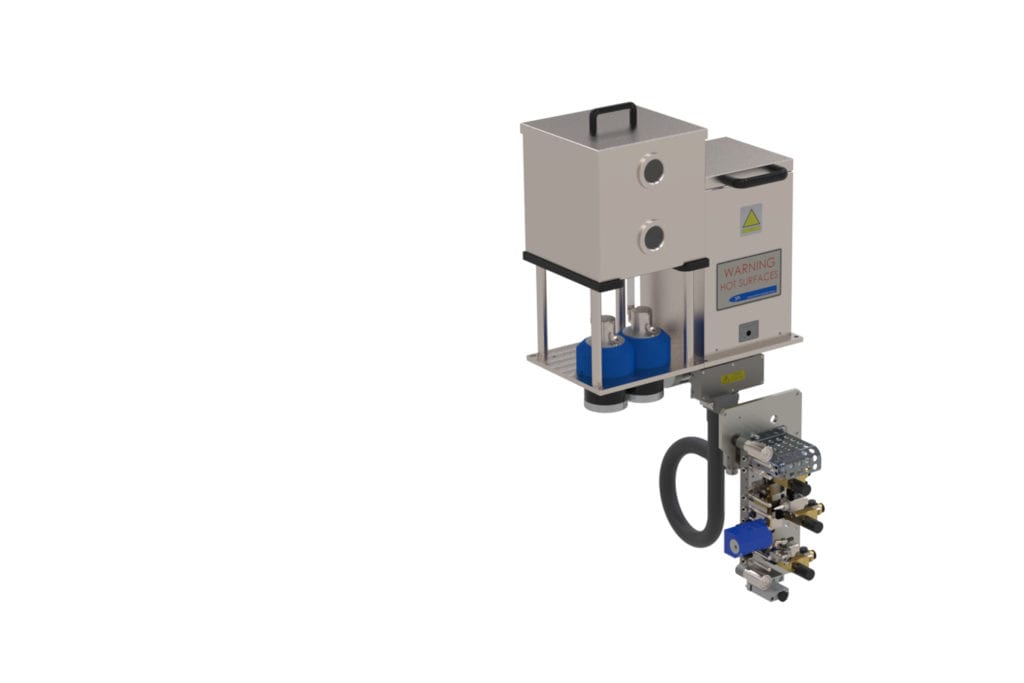
Innovative products and environmental drivers are creating new opportunities for adhesives even in a testing time.
By George Gay
SPI manager Danielle Roxborough appeared chuffed when I asked her in January what were the main factors driving the market for equipment used to apply tobacco industry glues. And she was chuffed; and the reason why she was chuffed turned out to be that while, in the past, the usual market drivers for such equipment have been cost reductions and efficiency improvements, currently, one of the main drivers was concern for the environment—and this she found pleasing. Of course, drives to improve efficiencies, especially, for instance, where they target waste reduction, can be seen as environmentally advantageous, but what Roxborough was talking about involved a direct link.
For various reasons, the major cigarette manufacturers are apparently showing renewed interest in finding an efficacious filter material that biodegrades more easily than does the most commonly used traditional filter material, which is made of cellulose acetate hardened with the application of triacetin. Of course, the search for more environment-friendly filter materials has been going on for a long time, which indicates that there are no obvious substitutes, but Roxborough said the industry was now investigating the use of crimped paper, and this was raising the possibility of some interesting developments in which ITM, a company that manufactures filter-making machinery and that is related to SPI through the Tembo group, was heavily involved. And, in turn, ITM had been approaching SPI because the efficient application of glue would be crucial in constructing such a filter and because SPI is the group’s acknowledged expert in respect of glues and glue application.
In part because of new regulations, such as the EU’s ban on single-use plastics, everybody was having to think about their products, the waste they produced and what effect they were having on the environment, said Roxborough, and so it was exciting to be involved in a new project such as this, especially since the group’s ethos was built around developing more environment-friendly products. It was exciting to see an environmental issue pushing developments, she added.
There are a number of reasons why paper has not been used more widely as a cigarette filter material, one of which concerns taste, and, again, this is an issue of interest to SPI, which is involved also in the development and supply of flavor application systems. The idea of using crimped paper as a filter material had thrown up problems, but, wherever there was a problem, there had to be a solution, said Roxborough; so one of the projects SPI had been looking at involved incorporating a filter-material flavor system onto production machinery. However, she added one important caveat. The idea was to try to make a paper filter that offered the same taste as did a traditional filter, when attached to similar tobacco rods. It wasn’t a case of trying to introduce additional flavors. It was about trying to give consumers products that tasted as close to those that they had become accustomed to but that had better environmental credentials. Inevitably, it would be something of a balancing act, but then, there was some resistance when plastic straws were replaced by paper ones, and people got used to them.
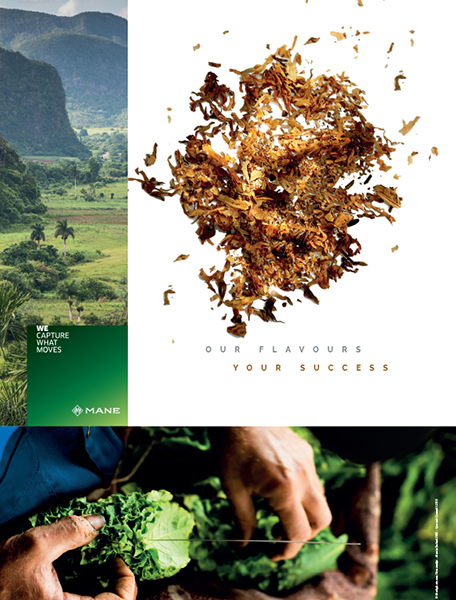
Transition to new products
Another factor driving the market for glue-application systems has arisen because of the transition being made from the production of traditional combustible cigarettes to that of more modern products, such as heat-not-burn (HnB) cigarettes. Clearly, while new, less risky products are seen as the future, their development is being funded in part by the income from the sale of traditional cigarettes; so the question arises as to how to keep existing traditional-cigarette production machinery running efficiently while avoiding the need to make major investments in new machinery that could be spent more wisely on developing new products. This situation, said Roxborough, had created an opportunity for SPI, which, by upgrading the glue-application systems on existing machinery, especially filter-making machinery, could greatly improve the efficiency of such machines at a fraction of the cost of a new machine. And as a consequence of this, SPI had seen an increase in demand for upgrades of glue applicators from gravity systems to pump systems. That had been a surprising knock-on effect of people wanting to reduce their investments in new machinery for combustible-cigarette production, she said.
Interestingly, while such a shift in investments is not directly aimed at protecting the environment, it may be seen as having such an effect. Switching a machine from a gravity-fed to a pump-system glue applicator is said to reduce waste, as, of course, does upgrading a machine rather than sending it to the machine graveyard.
The above market drivers come on top of one that has been around for a few years now and that was set in motion by the arrival of HnB devices. While many different next-generation products have been developed in recent years, for a while it looked like the market would be dominated by vaping devices, which offered few opportunities for SPI. However, with the arrival of HnB, things changed because, while these devices represented a clear break with the past, they were manufactured in ways that were reasonably similar to the production methods used for traditional combustible cigarettes. The arrival of HnB products opened the door again to opportunities for traditional tobacco industry companies because they used slightly different materials in slightly different ways, and what this meant in practice was that there was a need to rethink such things as glue application, Roxborough said. This might involve something simple, such as repositioning an applicator or reassessing how much glue to apply, but sometimes it involved a complete redesign.
The above, I think, gives an indication that whereas the tobacco industry has traditionally been seen as conservative, in recent years it has undergone huge changes. And this idea was underlined by Roxborough when I asked about what pieces of SPI’s equipment were the most in-demand. She replied that the answer to that question would depend on what week I was talking about, before going on to explain that, within the tobacco industry, little was predictable. Every year, SPI managers met to set targets for the year ahead and, while the overall targets were met, it was usually the case that the sales that helped the company meet those targets were of equipment different from the ones that had underpinned the predictions. This lack of market predictability was not necessarily a disadvantage, however, because SPI was flexible and its equipment was modular, so it could change direction quickly; it never became stuck in a position where it needed to sell a particular product.
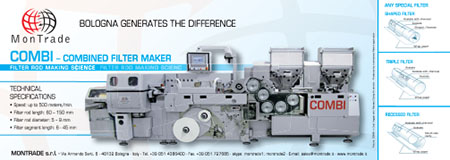
Riding the roller coaster
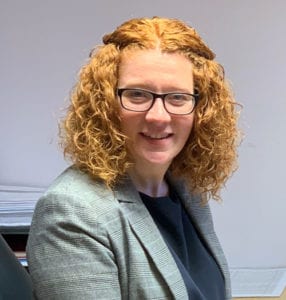
Of course, it goes without saying that 2020 was particularly unpredictable and, in answer to a question about how the Covid-19 pandemic had affected SPI’s business, Roxborough admitted that it had been a testing time—a roller-coaster year. The major issue that the company ran into was in March and April when it proved difficult to ship equipment. “We thought that the problem would be the supply chains,” said Roxborough, “but they were fine. But we were left with boxes that we couldn’t ship for three [weeks] to four weeks because some of our customers’ factories weren’t open.”
Still, SPI seems to have weathered the pandemic well. It has kept its factory open and fully functioning. It has not furloughed or made redundant any of its people, and neither has it recorded any confirmed cases of Covid-19. According to Roxborough, this success in the face of adversity has been down to the company’s being pragmatic. The first consideration was ensuring that people stayed well; so those who could work from home were sent home immediately while those on the factory floor were given an extra day off each week so that at any one time the factory could be kept running but with one fewer person in the building. And, of course, the more obvious steps were taken in respect of such items as masks and screens.
Infrastructure-wise, SPI was obliged to rethink its whole building, which was not necessarily a bad thing, said Roxborough. The company’s offices had become overcrowded and the pandemic forced it to have a clear out to create more space for people to spread out, something that had been under consideration since well before the pandemic struck but had never been implemented. Staff and the company have benefited too from another change that was implemented because of the pandemic—one that provided office staff with more flexible working hours and that meant the office is now open for an hour longer each day, a particular advantage since SPI works closely with Netherlands-based ITM.
Which subject brings us to Brexit. The U.K. concluded a deal with the EU shortly before it left on Jan. 1 after a year’s transition period, and I was interested to find out whether SPI yet knew how the new trading arrangements with the EU would affect its business. “In short, no,” said Roxborough. “We’re pleased there’s a deal; that helps, but we suspect there will be more administration. We’re shipping a unit this week to Europe and it has to go through more procedures in terms of paperwork and checking. But this is nothing new to us. We have been used to shipping outside Europe and we use a broker for imports and exports. We are going to monitor the situation cautiously for now and see what happens.”
When it comes to Brexit, SPI has the advantage of being linked to ITM, though Roxborough pointed out that the link-up wasn’t made because of Brexit. More than anything, the link-up had provided stability, which, in turn, was providing confidence about the future, she said. SPI still operated independently, but it had access to the facilities and know-how of a big group, and, at the same time, that group had access to SPI’s expertise.
The association with ITM has come in handy during the coronavirus pandemic because, while SPI’s engineers have been unable to travel, in some regions it has been able to call on local ITM engineers to help with equipment installation. However, what the pandemic had proved also, added Roxborough, was that SPI’s equipment was relatively easy to install. By using modern technologies and software, and by having dedicated teams on standby in the U.K., the company had been able to guide some of its customers through installation processes, both in respect of glue and flavors equipment. It was with some hesitation, she admitted, that the company started down the road of having its customers instal equipment, but it had worked out very well.
