The way forward
- Print Edition
- February 26, 2014
- 0
- 0
- 17 minutes read

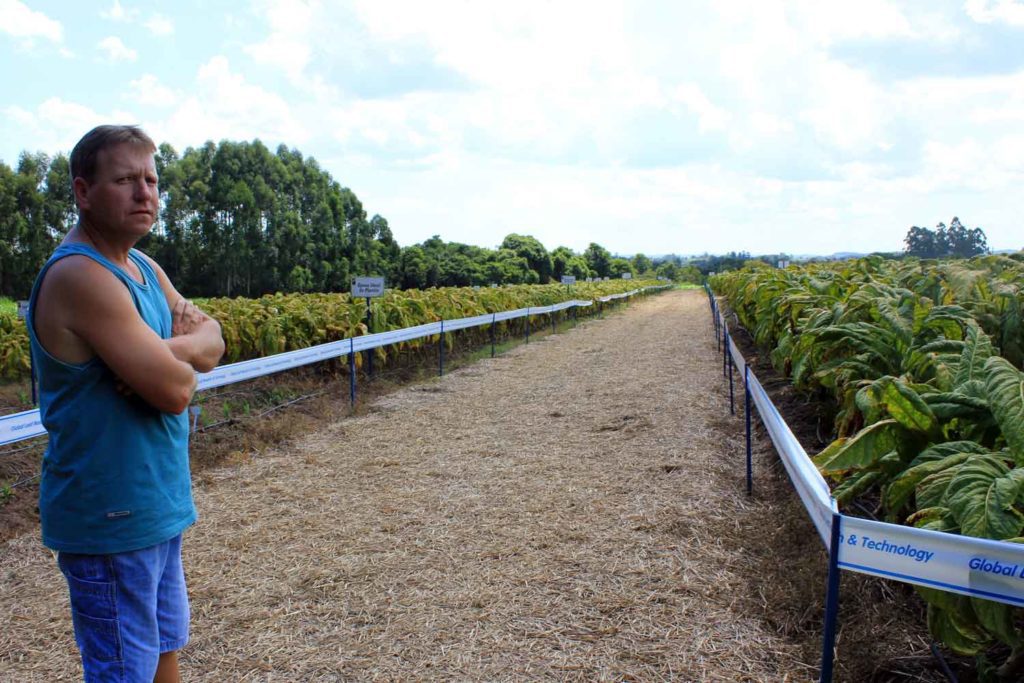
The Brazilian leaf tobacco industry cannot afford complacency in the wake of last year’s record earnings.
By Taco Tuinstra
There were lots of smiling faces in southern Brazil last year. At 706 million kg, the 2012–2013 tobacco crop volume may not have broken records, but its export earnings—the variable that counts—were unprecedented. According to Sinditabaco, an industry organization, leaf exports generated a whopping $3.27 billion last year. Can Brazil continue flying high? While generally confident about the future, industry leaders say several issues, including labor cost, must be addressed if Brazil is to sustain its strong position in the global leaf market.
Brazil’s reputation as a reliable supplier of flavor tobaccos is based on several factors, including the size of its growing area (large), its farmer profile (small) and the integrated tobacco production system (ITPS), which enables the industry to coordinate production with no fewer than 160,000 farmers in the states of Rio Grande do Sul, Santa Catarina and Paraná. Like elsewhere, tobacco growing in Brazil is subject to the whims of Mother Nature. But the spread of production over such a large area, with varying climate conditions and growing calendars, means that risk, too, is spread widely.
Planting takes place over six months, from May to November—a much longer timeframe than in the United States. And whereas some 75 percent of U.S. tobacco production is concentrated in the so-called Old Belt, the Brazilian equivalent—the area around Santa Cruz do Sul and Venâncio Aires—accounts for only a quarter of that country’s cigarette tobacco production. If one region suffers from adverse weather, conditions are likely to be better in other growing areas, and the overall impact will be mitigated.
That has certainly been the case this growing season. “At the end of September and the start of October, there were rains in the Old Belt, which delayed the tobacco’s development,” says Guilherme Steffen, regional administrative director, South America, at Alliance One International (AOI). “When the heat hit between Christmas and New Year’s, the plants were unprepared.” Other areas experienced more favorable growing conditions. “The Old Belt suffered a yield reduction of about 15 percent, but there was a slight increase in yields elsewhere,” says Aldemir Paulo Faqui, leaf production director of Universal Leaf Tabacos. “Taken together, the yield is down slightly over last year, but this is compensated for by the increase in area planted.”
The Brazilian Tobacco Growers Association Afubra predicts about 700 million kg in southern Brazil, including flue-cured Virginia (FCV), burley and Galpão Comum, a native variety.
Faqui expects quality to be decent, especially for burley. “The weather in the north of Rio Grande do Sul and the west of Santa Catarina—the primary burley-growing areas—was favorable for curing,” he says. “Humidity was high and there was no low temperature. We’re looking at nice, naturally brown colors for burley.” FCV quality is projected to be average this season.
Whether prices will be as firm as last year, however, remains to be seen. Farmers tend to respond to good crops by growing more tobacco—which depresses prices the next season—and this year was no exception. The area planted for the 2013–2014 crop was 3–4 percent larger than that for 2012–2013 (332,000 ha). Also, some traders believe the industry overpaid last year. This season, it will likely practice more restraint. On the bright side, the exchange rate is more favorable than it was in 2012–2013. “The less expensive real will make Brazilian tobacco more affordable for buyers,” says Gary Russell, sales director of Marasca.

Farmer profile
The ITPS has been a major contributor to Brazil’s success in the tobacco industry. Unlike its U.S. counterpart, the Brazilian leaf tobacco industry is dominated by small-scale production. The typical tobacco farmer in southern Brazil has 16.1 ha of land of which only 2.5 ha is reserved for tobacco, according to Afubra. Greater shares of his property are covered by crops such as corn (22 percent), soy (7.6 percent) and native forest (17 percent). But while accounting for a relatively small area of the farm, tobacco generates a majority (56 percent) of the average grower’s income.
Tobacco remains the No. 1 cash crop in southern Brazil, and contrary to the image projected by some anti-tobacco activists, Brazilian tobacco farmers are not impoverished or perpetually indebted. “Over the years, tobacco income has allowed farmers to buy consumption goods of a standard similar to that common in urban areas,” says Flavio Goulart, Japan Tobacco International’s (JTI) corporate affairs and communications director for South America.
But small growers generally don’t have access to funding from conventional financial institutions; they cannot fund their own operations like many U.S. farmers do—and that’s where the ITPS comes in. In the ITPS, tobacco buyers and producers work together to produce a consistent crop. At the start of the growing season, merchants provide their contracted farmers with finance and agricultural inputs, the cost of which are subtracted from the selling price after the crop has been grown. The dealer commits to buying the entire harvest, offering the grower a degree of security that he doesn’t get from other crops. Leaf technicians help the farmer follow proper agricultural practices, ensuring the buyer gets the tobacco styles he requires.
Traditionally, small-scale farmers have relied on manual labor, provided mostly by family members and neighbors. “These farmers can respond instantly to developments in the fields,” says Robert Jones, president of Tabacum. “They can reap and top at exactly the right time, which in turn promotes quality.” But small-scale production is ill-suited for mechanization—something that could become a problem as labor gets scarcer.
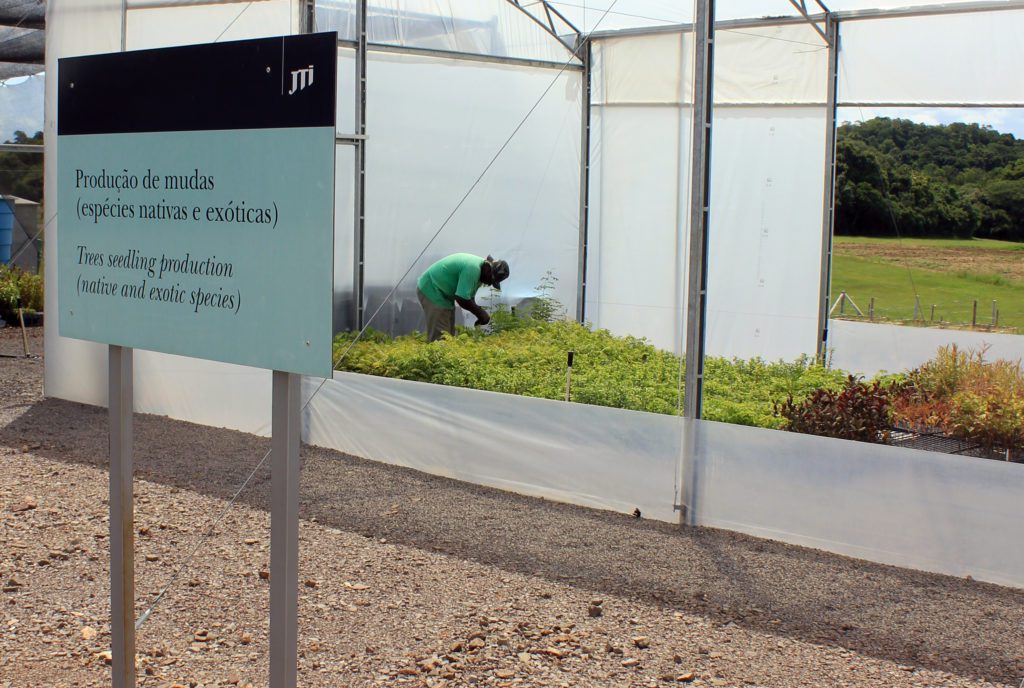
Booming Brazil
Migration to the cities has been an issue for decades in rural areas worldwide. In Brazil, the challenge has been exacerbated by the country’s recent economic boom and upcoming events such as the 2014 football World Cup and the 2016 Olympics, which have created strong demand for workers in construction and services. In December, Brazil’s jobless rate fell to a record low of 4.3 percent, according to the Brazilian Institute of Geography and Statistics—a figure that many economists equate with full employment. Adding to the problem, whisper some, are generous social programs, promoted by Brazil’s ruling Workers’ Party, which have reduced the incentive for people to accept relatively low-paying positions.
Meanwhile, a government push to formalize agricultural labor has made farmers even more reluctant to hire workers. Growers are now expected to prepare proper contracts, collect taxes, etc. “For the average tobacco farmer, the paperwork required can be intimidating,” says Mario Bender, production superintendent at Premium Tabacos do Brasil. Instead of hiring help, farmers may choose to reduce their tobacco plantings to an area that they can manage with their family. The situation has also created a bit of a competitive disadvantage for Brazil versus that other flavor market dominated by small-scale producers. “You can be sure President [Robert] Mugabe isn’t enforcing all the labor protections in Zimbabwe,” says Jones. Farmers’ representatives and Brazilian legislators are discussing amendments to the legislation that would allow tobacco growers to contract temporarily labor under less onerous regulations.
In a way, the pressures are also a result of the tobacco industry’s success in eradicating child labor. The tobacco industry in southern Brazil was started in the first half of the 20th century, largely by German immigrants who brought with them a strong work ethic. As was common in those times, parents expected their children to help out on their farms. In today’s world, of course, child labor is frowned upon, and the tobacco sector has worked hard to discourage the custom. For example, in order to obtain a growing contract, a tobacco farmer must now provide proof of his children’s school enrollment. It’s not just a token formality: At the end of the school year, leaf buyers will demand to see the children’s attendance records. In addition, Sinditabaco and individual tobacco firms run campaigns to discourage child labor and promote education.
Brazil’s 2010 census found that the incidence of child labor in the tobacco fields had declined by 50 percent over the previous 10 years, compared with reductions of only 20 percent in other sectors. Individual companies report even more impressive accomplishments. Carlos Palma, corporate affairs manager at market leader Souza Cruz, says all of the farmers his company contracts with send their children to school now.
But the success of such initiatives also means that tobacco growing has become a less obvious choice for farmers’ children when they grow up. Exposed to a greater variety of opportunities than their parents, rural youngsters are increasingly opting for careers elsewhere, reducing the influx of new blood into the profession. Since 2009, the number of farmers has declined by 20,000, and the remaining ones are having difficulties finding labor.
The Brazilian tobacco industry’s response to the trend has been twofold. On the one hand, it is educating would-be farmers on the potential of the business, demonstrating that, for adults, cultivating tobacco is a valid—and, often, lucrative—choice. On the other, it is trying to reduce farmers’ dependence on labor through mechanization, alternative curing technologies and good agricultural practices. Such measures have the added benefit of increasing quality and, thus, income.
Because harvesting is the most labor-intensive part of the tobacco-production cycle, most efforts are focused there. Leaf dealers have been experimenting with harvesting machines, but they’ve found it challenging. Manufactured in high-cost Europe and attracting steep Brazilian import duties, the equipment is too expensive for the average tobacco grower. Efforts to convince local manufacturers to produce harvesting machines have been unsuccessful because of the still-limited market. Some suggest that, in order for mechanical harvesting to work, farmers may have to purchase them collectively. Another option would be to create a system in which specialist harvesting service providers rent out their equipment and operators.
Scale is not the only challenge. Bender points out that mechanical harvesting would require changes to agricultural practices. For example, because machines are less discriminating than humans, farmers would need to start growing tobacco varieties with leaves at greater distances from one another. “Manual laborers can pick and choose exactly the right leaves,” he says. “A machine, by contrast, simply harvests everything at a certain height.”
With labor accounting for 54 percent of tobacco production cost, mechanization offers the greatest potential for savings. But there are other opportunities to reduce expenses as well. Over the years, tobacco companies have introduced numerous technologies, such as the float system and the loose-leaf barn, to help growers become more efficient—and thus more profitable. “We can’t control world leaf prices, but we can control our expenses,” says Valmor Thesing, administrative director of Universal Leaf Tabacos. The larger companies operate dedicated research farms where they experiment with new seed varieties and cultivation techniques. Universal says it has had considerable success with no-till tobacco cultivation. As a result of such initiatives, farm yields have improved significantly over the years.
Sometimes, innovation is simply a matter of questioning existing practices. For example, Philip Morris Brazil (PMB), which entered the leaf market in 2010, no longer requires farmers to bundle tobacco, which is a time-consuming process. In the past, when there was plenty of labor, the cost of bundling was immaterial, but times have changed. “The agronomy team asked our processing guys, ‘Do you really need leaf in bundles?’” says Eduardo Muller, manager regional agricultural programs for Philip Morris International (PMI). With some adjustments, it turned out they didn’t. Non-bundling has quickly gained acceptance among Philip Morris-contracted burley growers, and the firm plans to extend the experiment to FCV farmers this year.
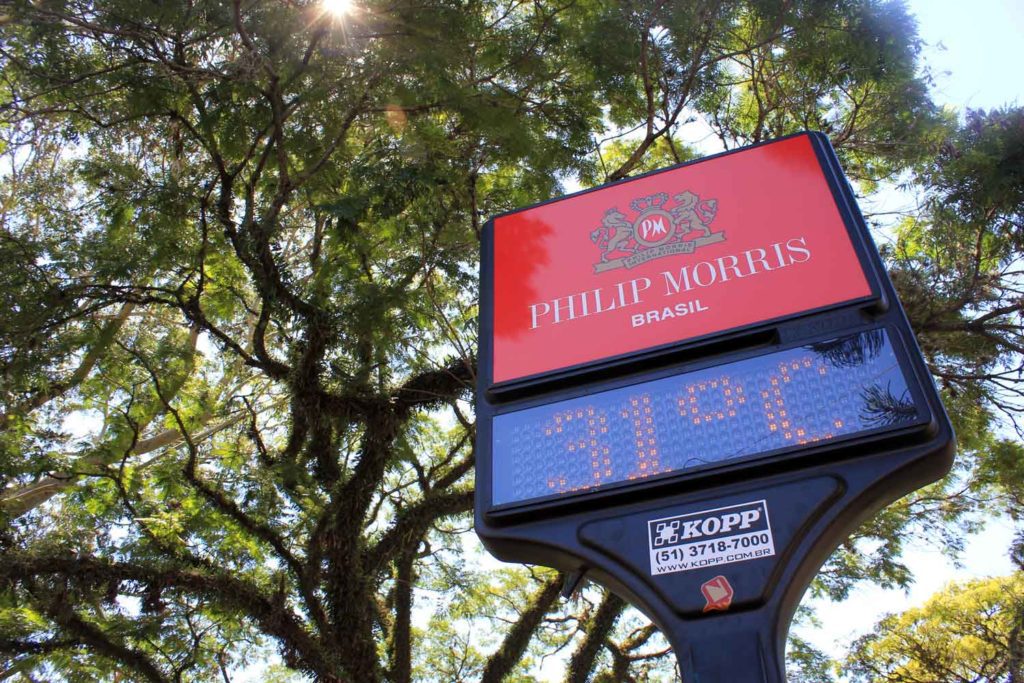
Vertical integration
Another significant development in Brazil has been the “verticalization” of cigarette manufacturers’ operations. Souza Cruz has sourced its leaf tobacco requirements directly for many years, but recently other manufacturers have gotten involved as well. Following several years of market volatility, JTI purchased the leaf operations of KBH&C and Kannenberg in 2009. The next year, Philip Morris International (PMI) acquired 17,000 farmer contracts from Universal and AOI, and created PMB’s tobacco operation.
“Our goals are to secure supply, be closer to farmers and take responsibility for the areas that we operate in,” says Goulart. “Vertical integration offers us an opportunity to apply the JTI way of doing things; we want to contribute to the standards.”
For the time being, both companies will continue working with leaf merchants. Without its own stemmery, PMB is still processing tobaccos at third parties. PMI also aims to buy part of its leaf requirements from other leaf merchants. JTI, too, wants a mix of third-party supply and direct sourcing. “We strive for balance,” says Goulart.
Not everybody is convinced of the wisdom of verticalization, however. Jones, an industry veteran who retired as CEO of Universal Leaf Tabacos in 2009, says many cigarette manufacturers were vertically integrated in Brazil during the 1980s, but then decided to divest their leaf operations to specialists. “Leaf sourcing is a high-cost, low-profit business,” he says. “It would not surprise me if, within 10 years, the manufacturers spin off those businesses again.”
For Universal and AOI, vertical integration has meant a shift in the emphasis of their activities toward processing, which generally carries lower margins than full-sales service. AOI has offset some of the lost PMI business by establishing a joint venture with the China National Tobacco Corp., called China Brasil Tabacos (CBT). Operating since January 2012, the JV has 6,000 integrated farmers spread over 41 municipalities of Rio Grande do Sul. CTB’s main customer is the Chinese monopoly, but the company will be selling to other customers grades that the Chinese are uninterested in.
While some have expressed concern about the large manufacturers “hoarding” tobacco, others see opportunity. Newcomer Tabacos Novo Horizonte (TNH), for example, has done well catering specifically to the needs of niche customers: companies specializing in roll-your-own or pipe tobaccos, for example. Created only three years ago, the firm has seen its volumes grow from 13 million kg in its first year of operations to an expected 23 million kg this season.
The market entry of firms such as TNH proves that, despite the adversity facing the tobacco industry, Brazilian tobacco leaf continues to generate considerable interest among businesspeople. Sinditabaco says it has added four companies to its membership since 2006—a remarkable gain in an otherwise mature industry. The challenges are real enough, however, and the sector will have to stay on top of its game to prevent last year’s smiles from turning into grimaces.
Using technology to optimize production
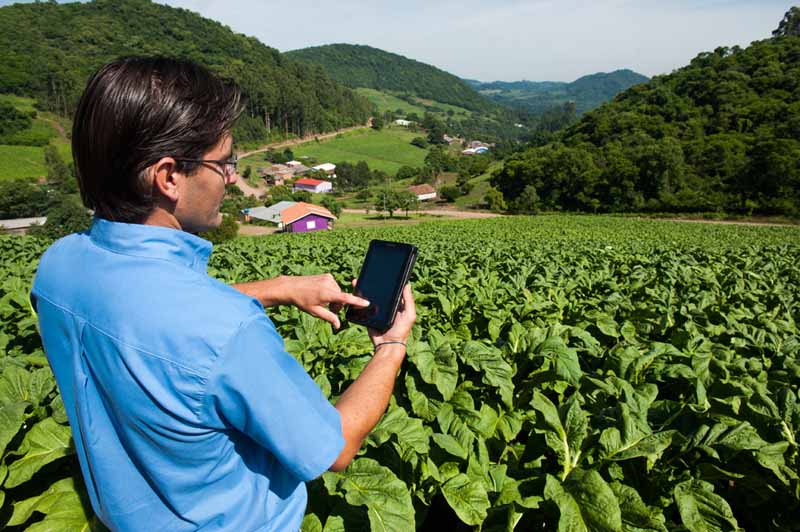
The size of Brazil’s tobacco industry never ceases to amaze. Leaf exporters coordinate their business with a whopping 160,000 farmers, growing a little more than 2 ha each and spread over an area larger than France. Just contemplating the logistics of supplying inputs, providing agronomic assistance and keeping track of crop development is enough to make the mind boggle. The task is further complicated by the fact that tobacco companies take on all sorts of social responsibilities, such as ensuring that farmers send their children to school.
Fortunately, technology is lightening the workload. Universal Leaf Tabacos has developed an application, Mobileaf, that allows the company to keep up with all relevant information in real time. Using tablet computers, the firm’s leaf technicians collect data from the fields about the area planted, soil types, reforestation and fertilizer requirements, among other variables. The gathered information is synchronized over wireless networks with a central database, allowing Universal to better plan its operations, respond faster to field developments and, ultimately, produce tobacco more cost-effectively.
Valmor Thesing, Universal Leaf Tabacos’ administrative director, says Mobileaf has greatly improved the quality of information. In the past, administrating relationships with the company’s 30,000 contract growers in Brazil involved lots of paper—with the associated risk of copying mistakes. Today, the risk of such errors has been virtually eliminated. Data flows faster, too. Whereas in the old days it could take up to four weeks for information to make its way back to the head office, updates are now almost instant. Brazil’s 3G mobile phone network is well developed, and even if a technician has trouble connecting from the field, he can still do so from home.
Conceived only three years ago, Mobileaf has caught on quickly. Universal is now preparing to implement the system in Africa, Italy and the United States. —T.T.