Riding high
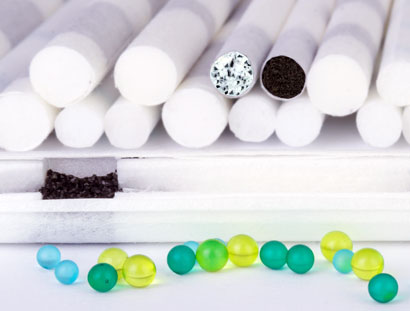
Aiger Engineering thrives as new products continue to disrupt the traditional tobacco business.
By George Gay
During an interview at the end of July, I asked Arek Druzdzel, Aiger Engineering’s business development director, if the tobacco machinery business had been tough in recent years, what with falling cigarette sales in many Western markets and much consolidation having taken place and still taking place within the tobacco manufacturing sector. His answer was illuminating. Yes, it had been tough, he said, but not for Aiger.
Aiger had been the fastest-growing tobacco machinery supplier, with an average annual growth of 18 percent during the past three years, he said, and this year it was promising to deliver a sales growth of 20 percent. Aiger would double its size before 2020, he added.
So, what is driving such growth? Ideas and their progeny: innovation. Indeed, Aiger says it is following a strategy aimed at positioning the company as the most innovative supplier of flexible machinery for the production of cigarette filters and cigarette packing, as well as the development of novel quality-assurance management systems, such as its Matrix Neo.
But the ideas and innovation don’t stop with traditional tobacco machinery; they stretch out to include heat-not-burn (HNB) requirements and to imagine a future with other next-generation products.
OK, every company says that it is innovative, but Aiger has some history in this respect. Aiger was formed 23 years ago, and Courtland Macduff, the company’s sales director for Asia, said that for most of its history the company had been working with multinationals on special projects—what he described as complex engineering projects. So there need be little surprise that in 2015 Aiger took home to its base in Plovdiv the award for Bulgaria’s most innovative company.
Focus on innovation
Perhaps something dynamic has built up in the air around Plovdiv, which has 8,000 years of history and which, from the end of the 19th century to World War II, was known unofficially as a tobacco city. In 2019 Plovdiv will enjoy being a European Capital of Culture, while today it is Bulgaria’s fastest-growing business, technology and economic center, attracting investment from international businesses and employing more than 100,000 people in the machinery and components sectors.
Aiger employs about 220 people at its 7,000-square-meter Plovdiv production facility (about another 20 people are employed at the Aiger Group’s Swiss base) that is set on a site of about 18,000 square meters. It has a diversified workforce within which most of its employees are designers and engineers with master’s degrees, but that includes also assembly and installation engineers, as well as fitters because it produces most of its mechanical parts in-house. The company sources its qualified employees mainly from technical high schools and universities in Bulgaria, and, three years ago, it started its own internal education program called “Aiger Professor,” which is based on the German model of hands-on training during the education of young professionals.
Aiger’s focus on innovation can be inferred from the fact that more than 50 of its employees are engineers working as part of R&D, mechanical, electrical and software teams. And, in turn, this focus on R&D and design reflects Aiger’s business, which is based on building customized, application-based equipment, including the types needed to produce specialty packs and complex cigarette filters.
Such equipment includes also that needed for the manufacture of HNB product components. Already, Aiger supplies a number of pieces of equipment for HNB production lines, such as filter plug platform machines and modular packers. However, it has been involved also in R&D, design and production projects for HNB base filter plugs.
Overall, Aiger supplies what it describes as a Flex-HNB-making platform—machinery elements into which a specific Flex platform has been integrated. “The benefit of using a proven process enables us to minimize industrial risks but mainly allows our customers to limit their investment risk by providing the possibility of reconfiguring machines to conventional equipment,” said Macduff.
While it does not provide any equipment for the e-cigarette sector, which, unlike the HNB sector, includes no traditional tobacco industry elements, Druzdzel said that, as an engineering-to-order company, Aiger would look at such developments if there were a partner or customer to work with.
Cross-fertilization
Again, Aiger has history here—in this case working outside the field of tobacco—experience that has allowed it to benefit from a cross-fertilization of ideas and that could help it in coming to grips with the challenges of developing machinery to manufacture next-generation products. Although 90 percent of its business involves the tobacco industry, it also builds specialized equipment for clients in the pharmaceutical industry.
“Currently, we focus on fine dosing small quantities of powder and granulate materials into small vessels and precise, on-line measurement of the dosed masses,” said Druzdzel. “This includes compliance to pharma regulations. Also, based on our experience in the tobacco industry, we build pharma-specific, bespoke inspection systems that allow for online registration of key parameters. Both industries converge as the search for successful new-generation products intensifies on both sides.”
HNB and other new-generation products certainly constitute one of the areas where Aiger sees its focus on innovation coming to the fore. “Look around,” said Macduff. “Everywhere you see new products that, through the application of new, exciting technologies, have advanced out of sight. There has been a sudden and fast rise of the driverless, electric car, and new tobacco products will move in a similar manner. By 2025, many people will travel in driverless cars, and most big cities will not allow anything but electric vehicles on their streets. Nobody can see into the future of the tobacco industry, but when HNB products are accepted by bodies such as main regulating administrations, international organizations and legislators as being, as claimed, more than 90 percent less risky than are traditional cigarettes, it is likely that soon these products only will be allowed to be [for] sale. It will be like the introduction of seat belts in cars—no ifs and no buts.”
At that stage, sales of these devices—and therefore sales of the equipment needed to produce them—will take off. And here again, Aiger is prepared—open for future challenges, as Druzdzel puts it. While most of the company’s employees are engineers, the sales team has recently grown to account for 10 percent of the workforce. Aiger has established offices in Brazil, Switzerland and the U.S. It has also recently opened a Moscow office and is in the process of reorganizing its Asia business, something that will involve the opening of another office, probably in Southeast Asia, by the end of this year.
And with sales agreed, Plovdiv is well-positioned geographically for Aiger to buy in the materials it needs and to send out its machines. The factory is about 3 kilometers from the nearest railway station and 2 kilometers from a major motorway that connects the airport in Sofia, Bulgaria, which is 140 kilometers away, with the Black Sea port of Burgas, which is 250 kilometers away. And there is a good international road network connecting Plovdiv with all neighboring countries and the rest of Europe.
Fast adapters
Aiger says its equipment portfolio is focused on two types of flexible and “fast-adapting” machinery: Flex filter makers and EON 300 cigarette packers. It offers a modular “plug and play” machine platform that allows operators to change from simple to complex filters in less than an hour. The Flex modules include those that can insert capsules, flavors and granular materials, and those that can process nonwrapped and paper filters. Each Flex module performs a dedicated function, such as inserting capsules (objects) into the moving tow or rod cavity, while, at the same time, handling the filter plugs and transferring them to an upstream module or to a desired position, defined by a final rod specification.
In addition, Aiger has developed a twin capsule inserter. The company says that the inserter offers a gentle and cost-effective method of including two different capsules—perhaps capsules of different sizes or containing different flavors—in a single rod, or cigarette.
Some Flex filter platforms, meanwhile, have been installed for development use in response to customer requests for unique modules to add to their existing complex-filter capabilities. “Moreover, we are introducing our bespoke micro-dosing solution for medical capsule-filling machinery,” said Druzdzel. “This opens a new chapter in the tobacco industry where extreme cleanliness meets extreme, six sigma dosing precision requirements.”
One of the things that Aiger keeps its eye on is what it terms “legislative drivers,” such as the EU’s revised Tobacco Products Directive (TPD2). The company says that it was the first in the market with a full-size modular packer—the EON 300—that could be converted from conventional to TPD2 compliant packs in two shifts. And down the line, it offers a TPD2-ready compact stamper that can be converted to or from TPD2 format within less than 2 1/2 hours.
“For packing, we offer a convertible, modular fast-fit system that allows customers to change from simple hinge-lid boxes to complex multichamber boxes—packs that are TPD2 compliant, and ‘Handy Packs’—in under three shifts,” said Druzdzel. “Packs include super-slims, 5-50s, round, square and everything in between.”
Handy Packs are hinge-lid packs with an inner divider. “We have a TPD2 compliant packer, the Eon 300, that allows inner-divider insertion to create two separate compartments,” said Druzdzel. “This is especially useful for [other tobacco products]. In fact, our most recent innovative machine is the versatile Eon 300 packer for Handy Packs and for MYO applications. This clearly demonstrates the flexibility of our Eon 300 packer, on which we can make a three-cavity box and then feed three different and complex-shaped items into the box.”
In fact, Aiger has recently sold the Eon 300 for producing limited-edition packs so that the consumer marketing teams of a large manufacturer can test new pack designs in limited production runs.
As is mentioned above, for quality assurance, Aiger offers its Matrix Neo, which reports via Scada, ERP-SAP or Microsoft Dynamics to ensure constant product quality and data on which management can base corrective actions. It has been installed on filter and cigarette machines to check for dimensions, density, photo recognition, carbon fill, and capsule placement and damage, with explicit management data reporting. Although Aiger no longer offers cigarette makers or rebuilt machinery, it says the Matrix Neo can be retrofitted to any single-rod maker.
Looking ahead, Aiger is intending to establish a new web shop for its established clients and to prepare for “Industry 4.0”—the fourth industrial revolution. “We have already achieved 90 percent-plus digitalization of all our data and systems,” said Druzdzel. “Aiger has recognized these ongoing processes and the associated business potential, and we have started preparing the company for these new realities.”
And it is already well-prepared. It has a young workforce, with the average age of its employees being 34—people Macduff describes as brimming with excellent, challenging design ideas and the software skills to implement them.