Beyond mechanization
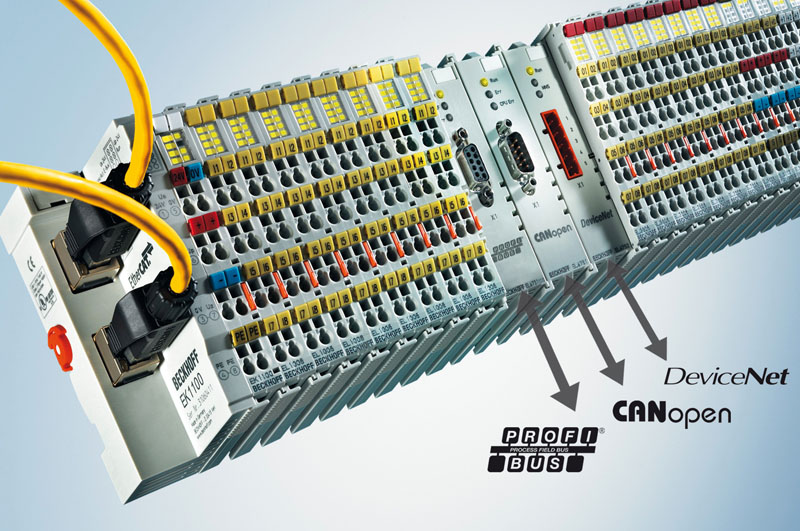
The potential and limitations of automation in the tobacco industry
By George Gay
There is what seems to be a fully automated system within my head that allows me to grasp what somebody is saying when they tell me they have just bought a blue car, even though they don’t provide information about the shade of blue. I have never understood how it works, but I seem to have somewhere in my brain a subconscious picture of a universal blue. I guess everybody does, so we are able to speak quite happily to one another about something being blue without having to be specific. In fact, it is only when we get specific that the disputes start. You turn up in your blue car and I complain that it’s green.
I was reminded of this when recently I started to speak with a number of people about automation as it applies to the tobacco industry. It was possible to talk about automation quite freely until, suddenly, you became aware that perhaps what was being discussed was not automation as you knew it, but mechanization, or the application of IT systems, or something else entirely.
Here is what Wikipedia has to say about automation: “Automation is the use of control systems and information technologies to reduce the need for human work in the production of goods and services. In the scope of industrialization, automation is a step beyond mechanization. Whereas mechanization provided human operators with machinery to assist them with the muscular requirements of work, automation greatly decreases the need for human sensory and mental requirements as well.”
This is a good, clear definition, but it raises some issues when applied to the tobacco industry. If we insist on including the reduction of human work within the definition—and I have to admit that my “universal automation” probably does make such an inclusion—how can we explain the fact that further automation is being applied to tobacco factories where the head count reached a minimum some time ago?
Head counts
I guess the first thing I should say is that nobody I talked with mentioned the idea of reducing the number of people employed, at least not without being prompted to do so. Certainly, Andreas Kuemperling, who is responsible for business development at Siemens, was fairly dismissive when I mentioned that favorite vision of the 1980s: the tobacco factory without people. Theoretically, he said, such an idea was possible, but in practice it wasn’t realistic partly because you were handling a natural product and partly because the equipment was not 100 percent reliable—failures were possible. Today, Kuemperling added, machines were already taking decisions based on the rules of automation and software was becoming more and more important, but the final decision had to be left to a qualified operator.
In fact, Tomasz Kramek, the business development manager at the Polish subsidiary of the ITM Group, made the point that in the recent past there had been instances where factory head counts had been allowed to rise slightly. Kramek, who was previously chief of ITM’s automation department, told me that 10-15 years ago there had been huge pressure, especially in respect of primary departments, to use every means of automation to reduce the number of people. But since then it had become clear that this was not always the best strategy because it could result in a reduction in the quality of the product.
Kramek made me sit up at this point. There was clearly a conflict if one of the goals of automation was the reduction of people, but the reduction of people in primary departments beyond a certain level—a level that automation could apparently support—might lead to a reduction in product quality. After all, product quality maintenance, if not improvement, must also be one of the goals of automation.
The difficulties arose in primary because it was thought at one time that the whole process could be controlled from a central room using sensors and monitors, Kramek explained. But this was probably a mistake—a step too far. Tobacco was a natural product and there was a need for experienced people who, from time to time, could touch the tobacco, examine it visually and smell it, and these were tasks that it was not possible to automate.
This is not to say that labor reduction is not an aim of automation in tobacco factories. The situation varies from plant to plant, with those in the West generally being already automated while some of those in other regions still operate using considerable amounts of manual labor. Even in the West, there is still potential to reduce head counts slightly in some factories, especially in secondary departments, though whether such reductions would be an economic advantage is a moot point. Increases in automation might allow for the reduction of people, but they might also require the substitution of less qualified people with those more qualified, which might mean that there was little change in the wage bill.
Skill levels also come into play in developing countries. Automation in these countries might be rejected on the grounds that particular factories do not have enough money to invest in such systems, and it might be rejected because of socio-political reasons, but it might also be a non-starter because of the unavailability of enough people with the skills to oversee highly automated systems.
The true benefits
So if there is no or little economic advantage to be had in reducing the number of people employed in a factory, why should a manufacturer introduce automation? Well, according to Kuemperling, the three main drivers beyond safety, which is a given, are productivity, efficiency and flexibility.
Flexibility? Again, I was pulled up. Surely, automation is about a lack of flexibility—about imposing on machines a set of rules to ensure they operate in a predetermined, repeatable way? Not so, said Kuemperling; each automation or IT system was only as good as its design, and whereas a good design had to be based on rules, it had to be capable also of handling exceptions. Automation systems, for instance, could aid brand changes, calculating, among other things, at what time new blanks had to be sent from the store to the machine. But such preplanning had to be capable of taking into account the fact that things could go wrong; that there could be a materials break and a machine shut down. So if, as part of a complex production plan, when you were dealing with 20-50 manufacturing lines, you had to reorganize your production, automation systems capable of communicating through all levels could help the production management make the right decisions, on time.
Planning and the organization of work flows were aspects of automation that were emphasized by Siemens, which, working across a very broad range of industries, has a portfolio of automation products that amounts to “several tens of thousands of components” and is able to offer the benefits of the cross fertilization of ideas from industry to industry. In fact Kuemperling made the point that in factories that were already highly automated, planning might be the one area where further automation was possible. There was room for such advances because planning was such a complex matter, he said. Whether you considered such planning to be automation or IT was a questionable point, he added, but it had to do with automation because you needed to generate real-time information and provide your planning to the machines.
Kramek looked at the idea of flexibility from a different angle. Manual operations could be seen as being more flexible, he said, but such operations could raise question marks over the security of the process. With manual operations there was always the danger of wrong components being included in products and the uncertainty of whether this had indeed happened. Either way, this could be an expensive exercise. Automated systems, on the other hand, provided a full track of what had been included, where and when. In this way, they could minimize or even eliminate such mistakes, thus offering savings, especially given that the payback time on some of the equipment and systems was as little as a year.
I find flexibility to be an interesting attribute of automation partly because I can remember the time when a reasonably observant smoker could notice differences between the cigarettes in a single pack that had been produced on a mechanized line. And, I know this is heresy but I quite like such differences, so I asked Christian Schulze, business development manager at Beckhoff Automation’s food, beverage and tobacco industry division, whether automation could be geared to produce, on the same machine, productively and efficiently, products that were different, one to the other.
I have to say that he wasn’t greatly enamored of this idea, pointing out that this was not what automation was about, but he said that in theory it was possible. It was now possible to use small stepper or DC motors to change the operation of the machine while it was running. That was really easy, he said, so it would be possible to produce products that were different one to the other.
Schulze though, was more interested in talking about the more practical sides of automation: the fact, for example, that it could be used to make existing machines faster and more productive while improving the quality of the output. This sort of thing was now possible because, using industrial PCs (IPCs), the cycle time or control time was 100 microseconds, 1,000 times faster than what could be achieved with a PLC. So, with more information, your product could be made a little better. Not hugely better, Schulze said, but perhaps 2-5 percent better in respect of material and energy usage and production speeds. Savings of even that magnitude, he added, given speeds of 400-800 packs a minute, by the end of the year added up to significant sums.
The reference to existing machines above is an interesting one because it can be applied to refurbishments, something for which Beckhoff’s systems are said to be ideal. Beckhoff, said Schulze, used open, standard systems, so it wasn’t necessary to change everything on a machine that was undergoing refurbishment. New technology could be added but, at the same time, old technology could be retained where that was appropriate.
Beckhoff uses its open systems to good advantage, also, in unifying technology. Exploring a further horizon of automation, Schulze mentioned how modern buildings—their heating/cooling systems, elevators and lighting, for instance—were automated using computer programs. And with Beckhoff’s systems it was possible to run the building and machine automation systems with the same program. This meant that you needed just one engineer to maintain the primary, secondary and building automation, so the major manufacturers, who currently used a separate engineer for their primaries, secondaries and buildings, could save on engineers.
And, of course, automation doesn’t have to be confined within your buildings. It can be used for tracking and tracing individual products once they’ve left the factory, something that was future technology 10 years ago but that is standard now, said Schulze. Such systems, he added, were possible with a PLC but were expensive, whereas Beckhoff’s technology allowed the cost to be reduced.
This I guess is automation on the grand scale, but automation can be highly valued, too, on the small scale. Kramek described how automation had been used to allow the expansion of the role of the lowly tobacco silo, without any physical changes being made to what essentially is a box. Whereas the traditional role of the silo had been to hold one type of tobacco, automation had allowed the inclusion of more than one type without mixing, and also the concurrent loading and discharge of different tobaccos from the same silo.
Some years ago, this would have made as much sense as my idea about using automation to make products different, one to the other, but with the burgeoning of product portfolios, it obviously has application in today’s factories. Kramek told me that whereas some years ago a factory might be operating with only two or three blends, some now had to deal with 100-150 different recipes. In some cases, the smallest order from secondary was for the production of 1 million sticks.
Perhaps in the end we will need automated cyborg machine operators to deal with such complexity—and of course it would help the cause if they were smokers.
1