The Test of Time
- Print Edition Technology
- August 1, 2021
- 0
- 15 minutes read
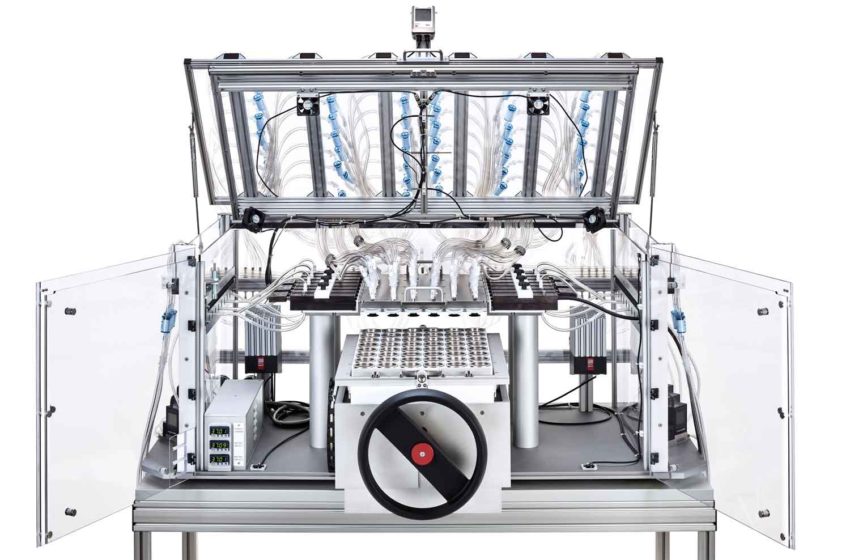
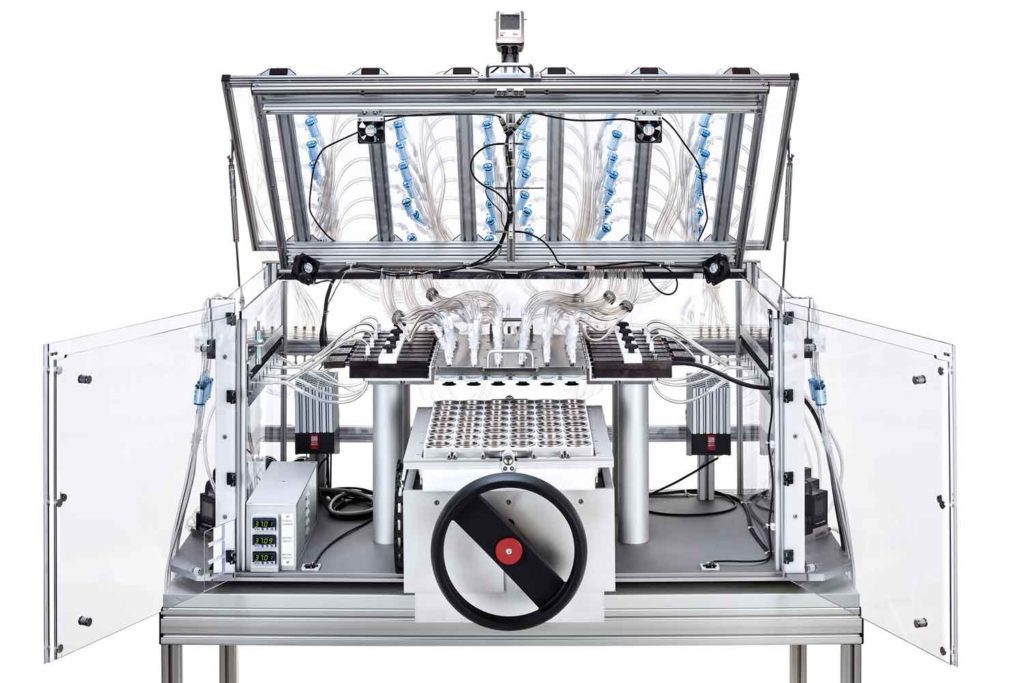
Regulations and next-generation products are driving demand for quality-control instrumentation.
By George Gay
It is well known that the arrival of new-generation tobacco and nicotine products has brought with it a need for new testing regimes and instruments. What is perhaps surprising is the smoothness with which these new instruments have fitted into and alongside portfolios of instruments designed with traditional tobacco product manufacture and testing in mind. Ian Tindall, of Cerulean, told me in June that he would struggle to name a product developed by his company during the past few years that did not have its origins or use profile in the new product categories such as vaping devices or heated-tobacco products (HTP). But, he said, this newly developed equipment had added to Cerulean’s range, from which very few pieces of equipment had been “retired.” All the legacy equipment had uses either in the combustible product sector or in the new product sector, and the newly developed equipment often had application in respect of traditional tobacco products. “[W]e have two-way traffic as far as instrumentation is concerned between new and established product use,” Tindall wrote as part of an email exchange.

All of the instrumentation companies TR spoke with in June, either in email exchanges or during telephone calls, cited the development of next-generation products (NGP) or reduced-risk products (RRP) as being, directly or indirectly, the main driver of demand for tobacco and nicotine sector instruments. Eric Favre, of Sodim, said, for instance, that instrument companies were having to develop equipment to measure additional product parameters linked to the complexity of RRP design. At the same time, he added, the need was increasing for the testing of emissions and the analysis of physical parameters in respect of hemp products.
Meanwhile, Tobias Krebs, of Vitrocell, said that, for his company, one of the main market drivers was the need for various organizations and companies to assess the possible impact on human health of the consumption of tobacco and nicotine products while another driver was the necessity of assessing in vitro data for submission to regulatory authorities.

While agreeing that the emergence of NGPs had been a driving force for instrumentation sector demand, Chris Crawley, of Axiom Select, made the point that this demand had required a significant investment in new instruments against a background of little growth. Indeed, he said, demand for traditional tobacco product instruments was flat and focused mainly on the replacement market and after-sales service.
This is not to say the replacement market is not important. Tindall said there was a perennial demand created by the need eventually to replace aging installed equipment and that this need could provide a steady “demand backbone” to an instrumentation business. Another driver, he said, was innovation, which could take different forms. On one hand, there were the sorts of innovations driven by instrument suppliers that might result in improved equipment that was faster, more accurate and easier to use, for instance, but that might otherwise result in solutions that provided for previously unrecognized needs.
On the other hand, there were the collaborative developments driven by the needs created by customer innovations. “The obvious example here is heat-not-burn products that require novel physical measurements of components and finished sticks, and also different methods of generating and capturing aerosols,” he said. “This has spawned new products and product configurations that are increasingly being deployed in factories ’round the world. Often, this demand is company specific and so generally the world does not see those novel instruments, but sometimes the opportunity exists to share these innovation-led products…”
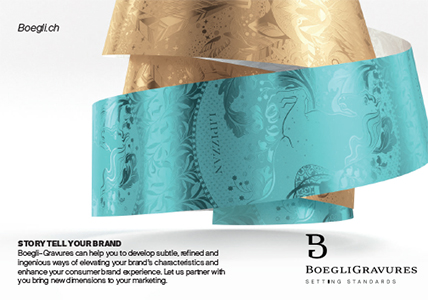
The Role of Regulation
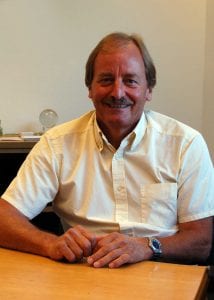
There was less agreement when TR asked what part regulations played in increasing or decreasing the need for instrumentation. Ian Benson, of Consultative Solutions, said he thought that regulation would only increase such demand, especially in relation to NGPs. Whereas this sector was not going to follow exactly the pharmaceutical path, traceability was increasing in importance, which meant more on-line measurements being made wherever tobacco was involved. Companies needed to know the exact nature of what they were making, and they needed to be able to recall what they had made, when, and whether it complied with regulations.
Krebs implied that by their very existence, regulators created a need because they were looking to obtain data on new products. And Favre said that regulation always played a significant role in the need for instrumentation and that this role would not decrease. The main role, however, remained that played by quality control, emission testing and scientific studies.
But Crawley said that while it might have been thought that all the tobacco regulations now in place and emerging would have benefited the instrumentation sector, the reality was quite different. For instance, the gathering of traditional tar, nicotine and carbon monoxide data from machine-based routine analytical smoking had actually declined—in some instances, quite significantly. Twenty years ago, some had seen the increased regulatory scrutiny as an opportunity to invest in independent laboratory testing facilities, but that market had still not materialized significantly.
Tindall managed to agree with both camps in saying that regulations could be seen as being a significant driver and as no driver at all. Much of the regulatory landscape around conventional tobacco use had been directed toward restricting use through such policies as taxation and plain packaging, and nothing in this had driven change in inspection and test equipment or a need for greater capacity. And while regulations that had been around for a while, such as those concerned with the U.S. Food and Drug Administration’s oversight of tobacco, had driven a requirement for increased testing capacity for emissions, that boom had already happened.
However, Tindall added, there were specific regulatory requirements in relation to HTPs that were driving a need for high levels of manufacturing controls and post-manufacture product verification, which seemingly could only increase. Where HTPs contained three, four or five nontobacco elements combined, the integrity and consistency of the final product relied on process control. And this had driven innovation in physical testing that was being carried out by, for instance, the X-ray machine and end form analyzer machines Cerulean released last year. The diversity of HTP designs demanded also that such test equipment was specific to each design.
Looking ahead, Tindall said that potential regulations might well increase the need for instrumentation. The very low nicotine proposals the FDA was considering might impact smoking machines while individual stick marking as proposed in the U.K. and EU single-use plastics legislation could all change the way the industry controlled and measured the products it made.
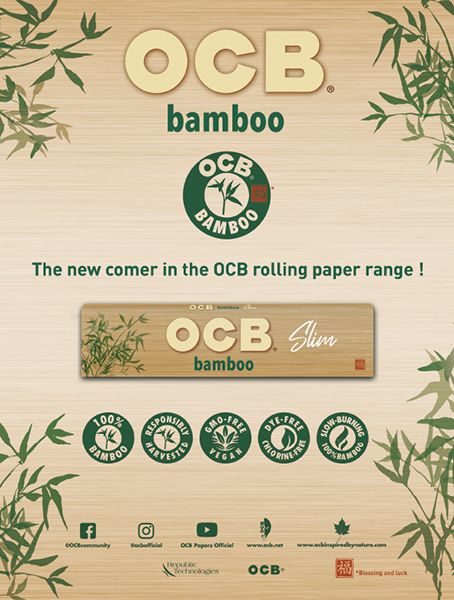
Trends
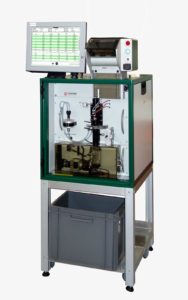
At this point, the question arises as to which tobacco and nicotine sector instruments are currently most in demand. And the answer, of course, largely relates to the specialties of the various instrument suppliers. For Krebs and Vitrocell, the answer was higher throughput exposure systems for the exposure of lung cell cultures and bacteria used in Ames tests because these instruments provided indications about the effects on human health of exposure to various compounds, and information on the relative exposure risks created by combustion and noncombustion products.
In addition, Krebs said that demand was high for dosimetry tools for assessing the composition of aerosols online, such as Fourier-transform infrared spectroscopy and time of flight mass spectrometry: tools that were required to assess the influence of compounds on biological systems.
For Favre, instruments for measuring physical parameters and those for measuring specific parameters related to emission testing were always in demand. And he made the point that since testing emissions from traditional cigarettes had a different set of requirements from those of testing emissions from electronic cigarettes, HTPs or hemp cigarettes, instrumentation had to be adapted as the market moved in these new directions. In addition, he said, upcoming regulation, either at a regional or global level, would intensify the need for new measurement solutions.
Tindall, meanwhile, said any equipment to do with HTPs was in demand, given that this was where tobacco company investments in new makers and production lines were being made. Physical testing required a whole range of measurements to be made and, usually, existing instrumentation was not suitable. Demand for smoking machines and vaping machines for e-cigarettes and HTPs had probably peaked with the deadline for FDA premarket tobacco product applications, but this demand for smoking and vaping machines remained strong and would probably continue to do so for a while. However, it was demand from multinationals and independent manufacturers for equipment for testing the smoke and physical characteristics of conventional cigarettes that still made up the backbone of Cerulean’s business.
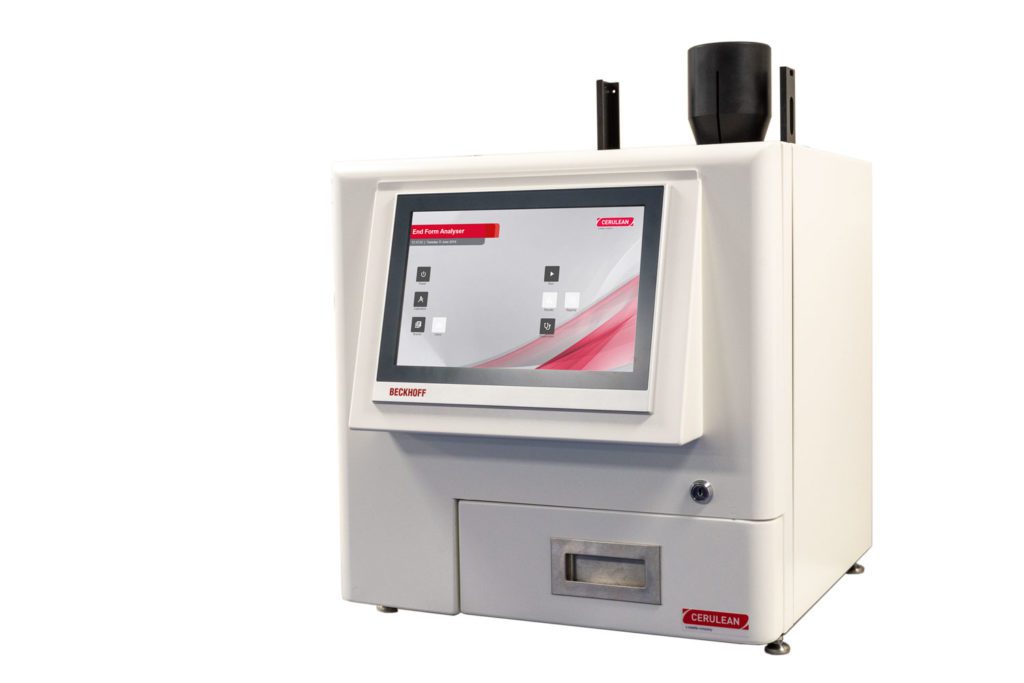
Matching Budgets and Needs
Of course, measuring processes, products and the potential effects those products have on health are all vitally important, but the question is, are the instruments necessary to carry out such measurements affordable? The responses here were diverse but tended to suggest what I guess is obvious. A big, rich company can afford instrumentation, whereas a smaller, less well-off one might not be able to do so. Crawley said that tobacco quality control and quality assurance instruments comprised a specialist market segment and, as a result, had always been expensive. “For example,” he said, “even manual digital instruments to measure diameter, pressure-drop and/or dilution cost $20,000–30,000 and are often considered unaffordable by the smaller independent producers. A multi-parameter test station can easily cost $100,000.”
Krebs, too, conceded that it could be expensive for small companies to carry out the sorts of testing for which his company’s instruments were designed. But, he added, the expense was less associated with the investment in such instruments than with that necessary in providing the infrastructure, such as laboratories, personnel and laboratory routines. One way this could be overcome, and often was, was to outsource such work to contract research organizations.
Favre, meanwhile, implied that such instrumentation was generally affordable, but he came at the question from the point of view that the measurements such instruments provided were an essential part of manufacturing processes rather than add-ons or luxuries. Such instruments, he said, were needed to help control quality during the production process and thereby help to ensure compliance with regulations but also to assist with research and development.
Tindall generally agreed with this idea, saying it was a truism that it was easy to measure the cost of quality checking, but the cost of poor or inconsistent quality was only measured eventually in lost sales and opportunities. However, he added that Cerulean was aware that different organizations had different objectives and resources when it came to investing in instrumentation and that it was important to have a product portfolio that reflected this—a continuum of equipment to match budgets and needs.
Tindall also echoed Krebs’ comments in saying that while the entry costs for the analysis of smoking and vaping emissions could be high, the investments necessary were inflated by the infrastructure needed rather than the equipment. And he, too, pointed out that one way around this situation was to take advantage of contract research laboratories.
Upgrades and Refurbishments
Given that there are at least some issues to do with affordability, it has to be asked, too, whether there is a viable secondhand market in tobacco and nicotine sector instruments or whether there is a viable refurbishment business. Well, according to Crawley, for the most part the major instrument manufacturers have never entertained a serious interest in the secondhand instrument market. Managements considered the sector not large enough to warrant serious consideration, he said. It saw no commercial advantage in the sector and concluded that it detracted from potential new instrument sales. However, for enterprising individual businesses, this market gap provided a wonderful opportunity—albeit not a large one—to supply quality services and products for about a third of the normal cost.
I think it need come as no surprise that the sort of instrumentation provided by Vitrocell doesn’t lend itself to the establishment of either secondhand or a refurbishment business. Elsewhere, such businesses do exist, but mainly they provide for internal use. So, Favre said, “secondhand” equipment might be transferred by a supplier from one manufacturing company facility to another while refurbishments were often driven by environmental or sustainability considerations. Refurbishments in the guise of upgrades might be driven by new technical requirements, such as software or controller upgrades, or by new measurement requirements. One particular upgrade might see an instrument designed for use with conventional products converted to one used for HTPs.
Refurbishments and upgrades, meanwhile, have become a fairly major offering from Cerulean—part of its culture. There was a lot of equipment in service around the world, said Tindall, and factories had made significant investments in this equipment. So, during the past two years, Cerulean had been examining how to extend the life of it by providing a range of upgrades intended to modernize equipment. This was in addition to a long-standing refurbishment service for physical test stacks that had generally been taken advantage of when customers cascaded equipment from one plant to another.
