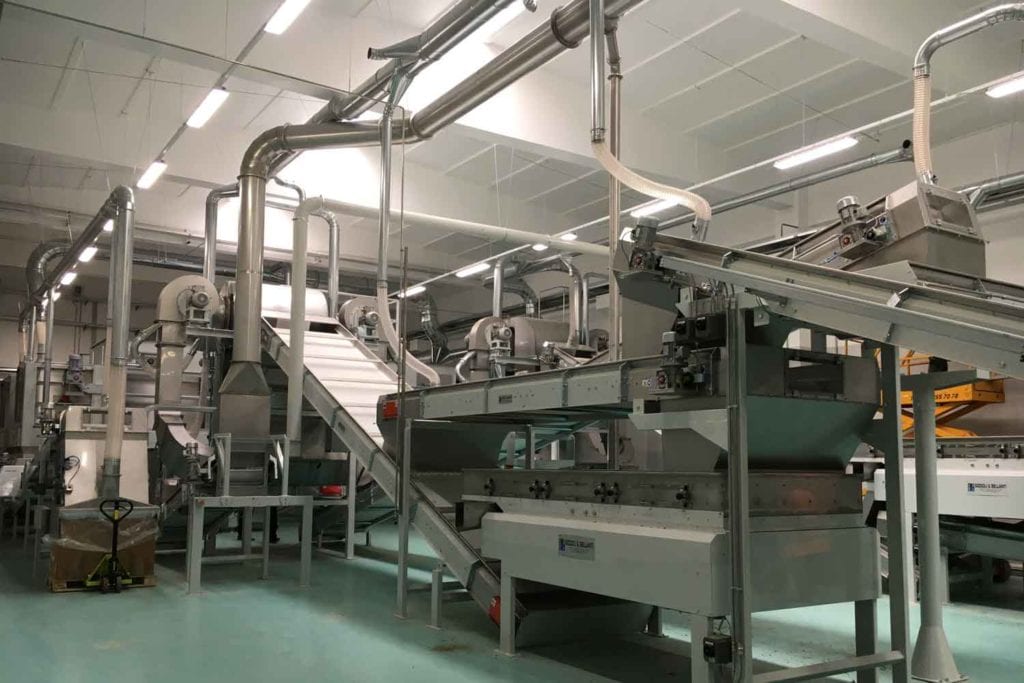
Machinery makers are investing to future-proof leaf processing factories.
By Stefanie Rossel

While global cigarette consumption has continued to decline for years and next-generation products (NGPs) take an ever-greater share of the nicotine market, there has been some motion in the market for primary equipment recently. British American Tobacco, Montenegro-based Novi Duvanski Kombinat Podgorisca and Alliance One Tobacco Argentina are about to build new processing plants or are relocating their leaf-processing sites.
“Without a doubt, the trend and investment are still toward heated-tobacco products [HTPs] and NGPs,” observes Ed Wozniak, regional sales manager at CPM Wolverine Proctor, a specialist in tobacco thermal processing operating from the U.S. and the U.K. “The consolidation, and in some cases diversification, of some plants is still ongoing.
“I say ongoing, as the relocation of plants has been there for some time. It is only logical to move or consolidate production to areas that provide a more economical production and/or are also located close to the remaining major markets for traditional tobacco products.
“This manifests itself in site and engineering service requests, along with the opportunity to upgrade and future-proof equipment as far as possible. This not only means replacement of spare parts and components but the addition of multiple sensors and up-to-date programmable logic controllers [plc].
“These key elements combined offer a wide range of opportunities to processors and benefits ranging from almost full auto adjustment ‘on the fly,’ which inevitably leads to optimized production costs, to real-time traceability of materials.”
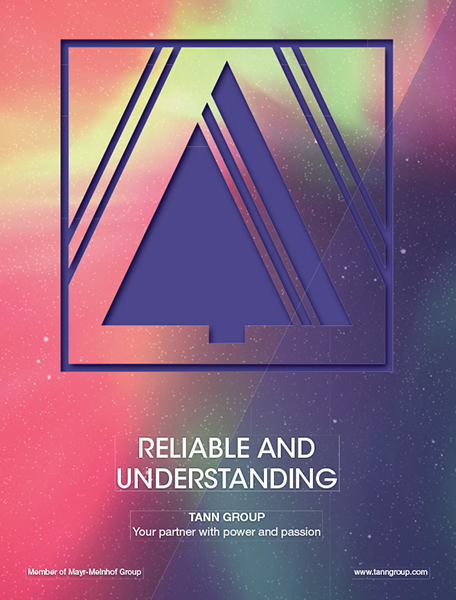
According to Wozniak, HTP sticks have to some degree eliminated the need for burley toasters, with most of the chemical process taking place in the stick. “Diversification and consolidation of the drying process into one flexible unit will possibly make the individual leaf, strip, toaster, stem and oriental dryer generally less attractive, presenting a new opportunity.”
Lorenzo Curina, sales director at Godioli & Bellanti, an Italian supplier of leaf-processing equipment, has also witnessed an increase of investments in the primary sector. “The primary, having a higher level of technology than a normal green-leaf threshing line, is the first link in the chain, which, in order to remain at a good level of quality and efficiency, needs to be modernized. We are not a big company, but we know how to offer adaptability, flexibility, leanness and of course state-of-the-art technology. And we have been called and invited to collaborate in the relocation and/or modernization of parts of the department of leading cigarette manufacturers.”
Stefan Hahn, managing director of Koehl Maschinenbau, a Luxemburg-based supplier of tobacco processing and logistics equipment, would like to see the investment pace accelerate. “The market situation slowly improves again, but not as fast as we would like to see as a supplier of processing machinery. Last year’s developments showed us the importance of interconnected solutions inside production. Ever since the beginning, we have been supporting our customers in the improvement of their plants, on the mechanical and automation side. Additionally, new processes lead us to the development of new solutions to react to the new market trends.”
If HTPs grow exponentially in the next years as is expected by leading cigarette manufacturers, Hahn expects upgrades and extensions of leaf-processing equipment to become more important as well. “Considering this, we see the opportunity to increase our delivery of such processing equipment. Koehl is already deeply involved in the manufacturing of HTPs with several different processes and machines.”
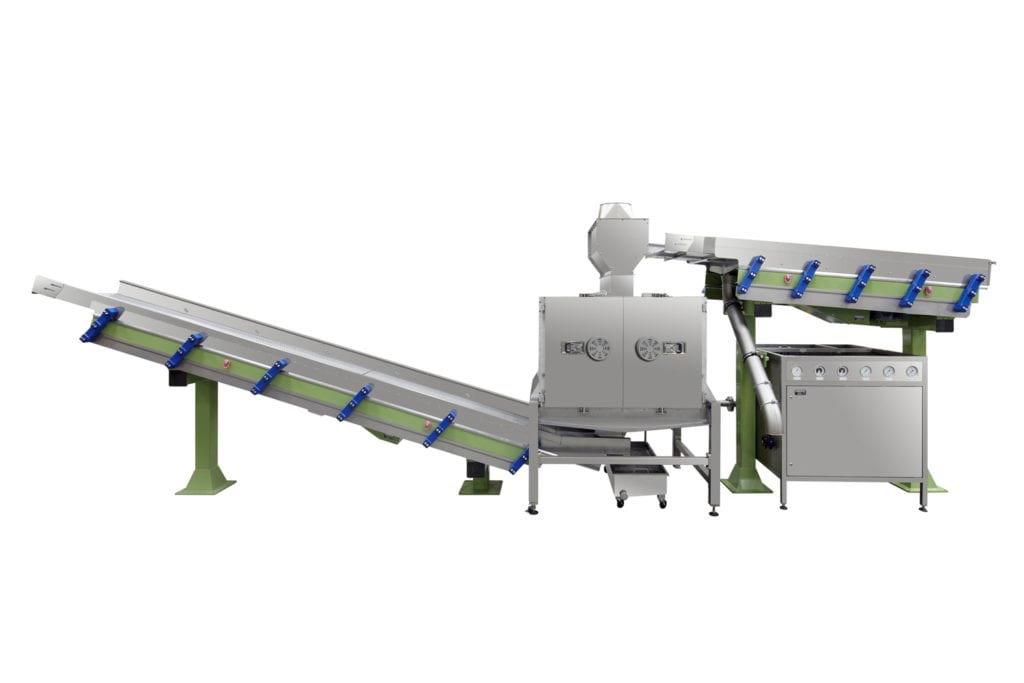
Coping with Covid
While in 2019 investments in the primary sector declined as cigarette manufacturers focused on next-generation products and integrating the track-and-trace technologies required by the European Union’s Tobacco Product Directive, the Covid-19 pandemic presented its own challenges.
“To save their production, all manufacturers at the beginning of Covid-19 just kept their ‘business-critical’ projects alive. Our development of a Covid-19 strategy to fulfill highest hygiene requirements and the benefit that Koehl has [with its] different affiliate locations made it possible that new projects were and still are feasible to realize. Therefore, of course the insurance of the project realization despite Covid-19 has become a major requirement for all customers.”
The execution of projects, he says, became more difficult because of travel restrictions. “To support our customers and avoid delays, we improved remote service activities, also with the help of our affiliates in different countries. Furthermore, we have extended our software of standardized machines with intelligent data-logging to guarantee improved online support.”
Curina says that the pandemic affected investment in the leaf-processing and primary machinery segments. “But mostly in the first period of the invasion of this cursed pandemic. Those investors who continue to see a source of income in tobacco know that the pandemic will not last forever. So we have noticed an almost unexpected revival of the market.”
Wozniak points out that with two or even three lockdowns in some countries, it will take time for these effects to be felt by the industry. “While the marketing information indicates that the global decline for cigarettes has been halted during lockdown—in the U.K. [smoking] is reported to be 7 percent up during lockdown—it does not mean that decline will not continue again when restrictions are relaxed. We can only follow our customers’ demands, and at this stage, we do not see any major changes filtering down to our level. I think that the level of cautiousness at this stage is understandable. We need to understand the real trajectory of the market as we emerge from Covid-19 restrictions and then we and the tobacco companies will have a clearer picture.”

Eliminating human error
Manufacturers agree that customer requirements for primary equipment are changing. “What is constantly required from us is the supply of machines with a low environmental impact, with minimal energy consumption,” says Curina.
“Without a doubt, the ‘smart factory’ or even Industry 4.0 ‘dark factories’—i.e., fully automated, unmanned factories—are being considered,” says Wozniak. “Integration of our equipment via our local plc system to a central control SCADA or similar [system] is now commonplace. The reduction of human error and having absolute control of as many process variables as possible is now paramount. It reduces overall operating costs and increases efficiency in many areas, as well [as] introducing real-time traceability of the product, in any part of the process. The need for this automation is the reason that CPM has within its divisions Beta Raven, which specializes in such integrations, and locally programmers and qualified electrical staff.”
Hahn confirms that customer focus has shifted toward a higher level of automation. “Therefore, we are proud to participate in several ‘smart factory’-related projects in which we are, together with our customers, developing tailor-made solutions to be prepared for these future trends. Here we see that specifically manufacturing execution systems—the intelligent link between the business and manufacturing levels—are extremely valuable overall systems for a smart digital transformation to increase efficiency, improve product quality and reduce costs. Our systems provide the correspondingly important layer for the direct execution of production orders as well as dynamic reaction to changes in orders, machine states, quality checks and similar situations for the self-organized factory.”
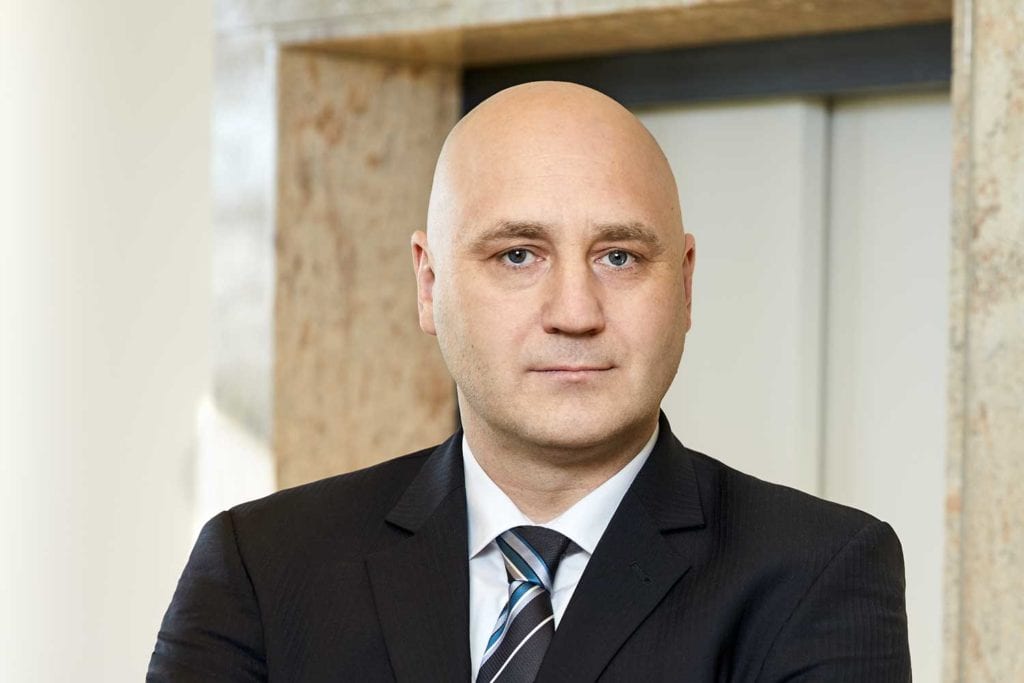
As the tobacco sector slowly transitions away from combustible cigarettes, equipment manufacturers have begun to eye other business opportunities as well. Valued at $24.6 billion in 2020, the global legal cannabis market holds considerable promise. Grand View Research expects it to expand at a compound annual growth rate (CAGR) of 14.3 percent from 2021 to 2028.
“We are following with interest the developments in the world of hemp for pharmaceutical and therapeutic uses and purposes,” says Curina, whose company also includes a processing business for herbs and plants, food and biomass but who insists its main focus will always be tobacco. “The openings are slow, but there are some,” he notes. “Openings depend on the political and social choices in the various countries. However, we pride ourselves in having created the first industrial processing line for hemp for about 1,000 kg per hour. And we were very happy when we learned that the processed product is appreciated by European pharmaceutical companies.”
Two years ago, Koehl launched an entire cutting line for cannabis. “This booming market is still interesting for us,” Hahn explains. “We were able to further expand and develop the cutting line over the last year. The hemp line is using Twister technology for hemp-moistening before cutting. We can now announce that Koehl has further projects in this sector.”
As part of the CPM Group, which is based in a U.S. state where marijuana remains illegal, CPM Wolverine Proctor is not allowed to offer dryers for cannabis containing more than 0.3 percent of THC, the psychoactive substance in cannabis. But the use of marijuana for medicinal use is now legal in 36 states and growing, Wozniak points out. “This may change things for us in the future. However, we can still offer dryers for hemp, which traditionally is used for sisal twine and rope and now also for high-end wearable fabrics similar to bamboo fiber. Traditionally, we have always been diverse, with dryers for fruits, vegetables, herbs, chemicals, cellulose fiber and ovens for breakfast cereals, ready meals and many more products. Many unique features in our tobacco dryers have actually come from some of these industries.”
